DER-IC University of Birmingham
The University of Birmingham’s DER funding has been used to construct a production line for recycled sintered magnets with an ‘end-to-end’ supply chain to enable a UK supply of recycled rare earth magnets from processed oxides. Currently, there is no capacity for sintered magnet manufacturing in the UK, and this new equipment provides a platform to secure a strategic supply of NdFeB alloy powder which can be fed into any part of the value chain from chemical, alloy production or directly into magnet manufacture.
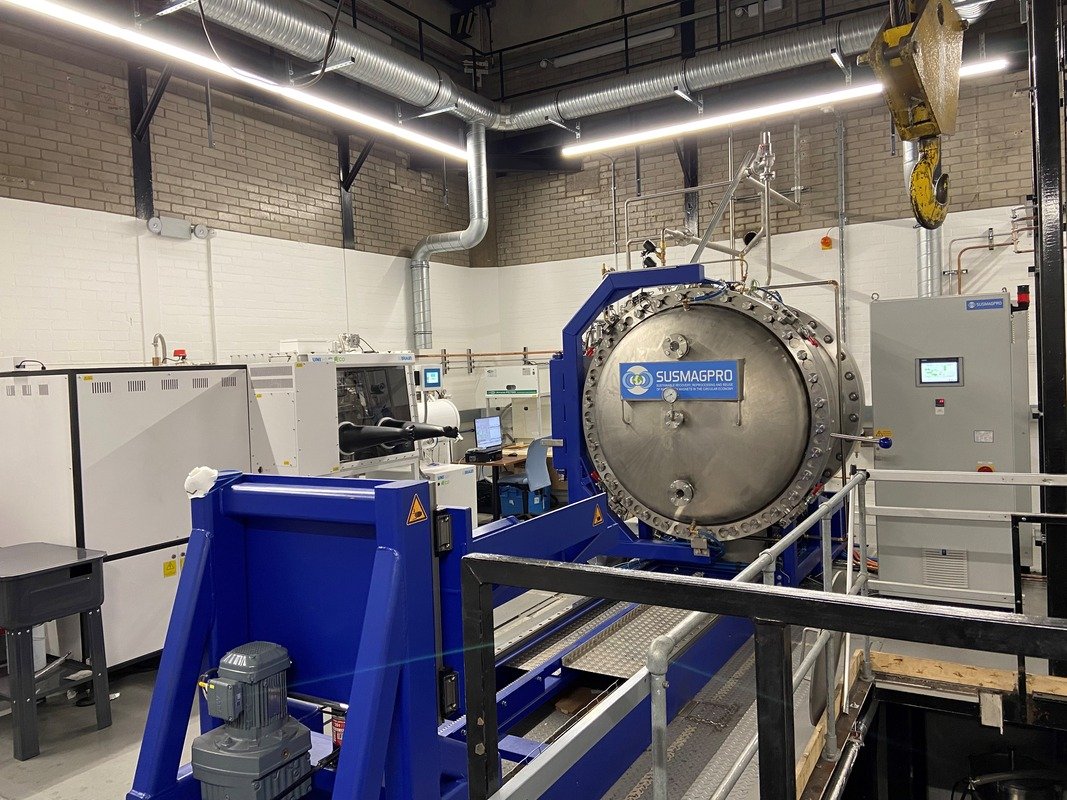
A range of advanced and highly unique equipment to enable the sensing, sorting, separation, purification and re-processing of rare earth permanent magnets. The equipment will include pre-processing equipment (cropping machines), a hydrogen reactor >2000 litres, powder processing unit including sieves, jet mill and blending system, magnetic aligning presses (uniaxial and transverse), pellet press and sintering furnace. The equipment can also be used to process primary rare earth cast alloys.
A range of machining and finishing equipment for REPMs including an EDM and grinding equipment.
This includes; 2 permeameters running up to 200°C, and 2 VSMs (to measure the hysteresis loops of solid and powdered magnetic samples), particle size analysis, 3-D magnetic scanner, kerr effect microscopy and chemical analysis equipment (ICP).
This includes high velocity ball mills, glove boxes, pulse magnetiser, isostatic presses and sintering furnaces for sample sizes between 10-50 grams
DER-IC CSA Catapult
The CSA Catapult in Newport, Wales, is a recipient of DER-funded equipment, with a focus on materials and components. The new equipment will address supply chain challenges with high power density and high temperature device packaging.
Compound Semiconductor Applications (CSA) Catapult Advanced Packaging Prototype Facility
Ceramic 3D printer for device packaging
- Ceramic 3D printer
- Thermal optimisation
- Ceramic debinder furnace – ceramic post process
- Ceramic oxide oven – post process
- Ceramic sintering furnace – high temperature ceramics
- Cleaning station
Metal 3D printing:
- Metal 3D printer (e.g. Copper)
- Printing materials supply
- Metal debinding oven – debinding process for package
- Metal sintering oven – sintering process
Metrology and processing tools:
- Tensile testing equipment – device quality check
- Fully automated Vickers micro hardness tester – device quality check
- Laser cutting / drilling machine – device processing for novel package design
- Lapping and polishing machine – device polish / lapping for preparation
- Density / volume measurement for 3D object
DER-IC Swansea University
Swansea University’s Centre for Integrative Semiconductor Materials (CISM) has received a £5m investment from DER to create a wide band gap power electronics component industrial pilot line. The pilot line will also be part of CSconnected, the world’s first compound semiconductor cluster based in South Wales. The new equipment will be housed in CISM at Swansea University’s Bay Campus in bespoke ISO 5 and 6 Cleanrooms.
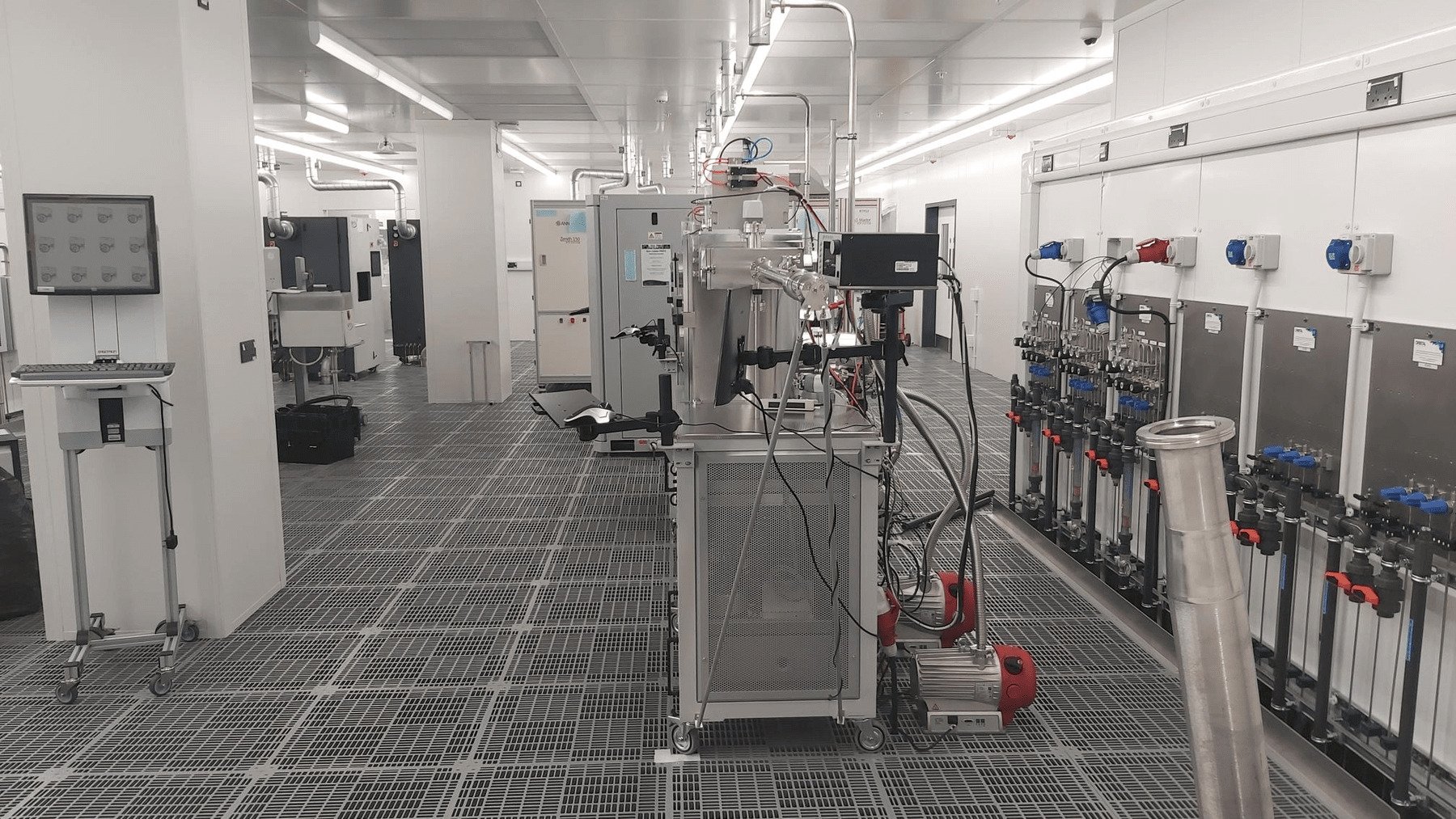
The pilot line will include:
- Advanced lithography – photo and nano-imprint
- Advanced etch – synapse deep dry etch
- Advanced deposition – dielectric and metal
- Backend – rapid thermal and laser anneal, wafer dice and grind