DER-IC Newcastle University
DER-IC Newcastle University is equipped with DER-funded Power Electronics and Electrical Machines assembly lines. Individual processes are representative mid to high volume manufacturing, are highly reconfigurable, and incorporate in-process inspection to enable process development, optimisation, and verification. Assembly is supported by dynamometer, X-ray and CT scan, and environmental test equipment.
Power Electronics Assembly Line
Located within a cleanroom environment, state-of-the-art, flexible, industry-representative equipment enables custom packaging of silicon die, devices and circuitry, and surface mount circuit board manufacture and inspection, providing a platform for the development and scale-up of advanced manufacturing processes for highly-integrated power electronic systems. Specialist inspection and diagnostic equipment enables verification of manufacturing process quality.
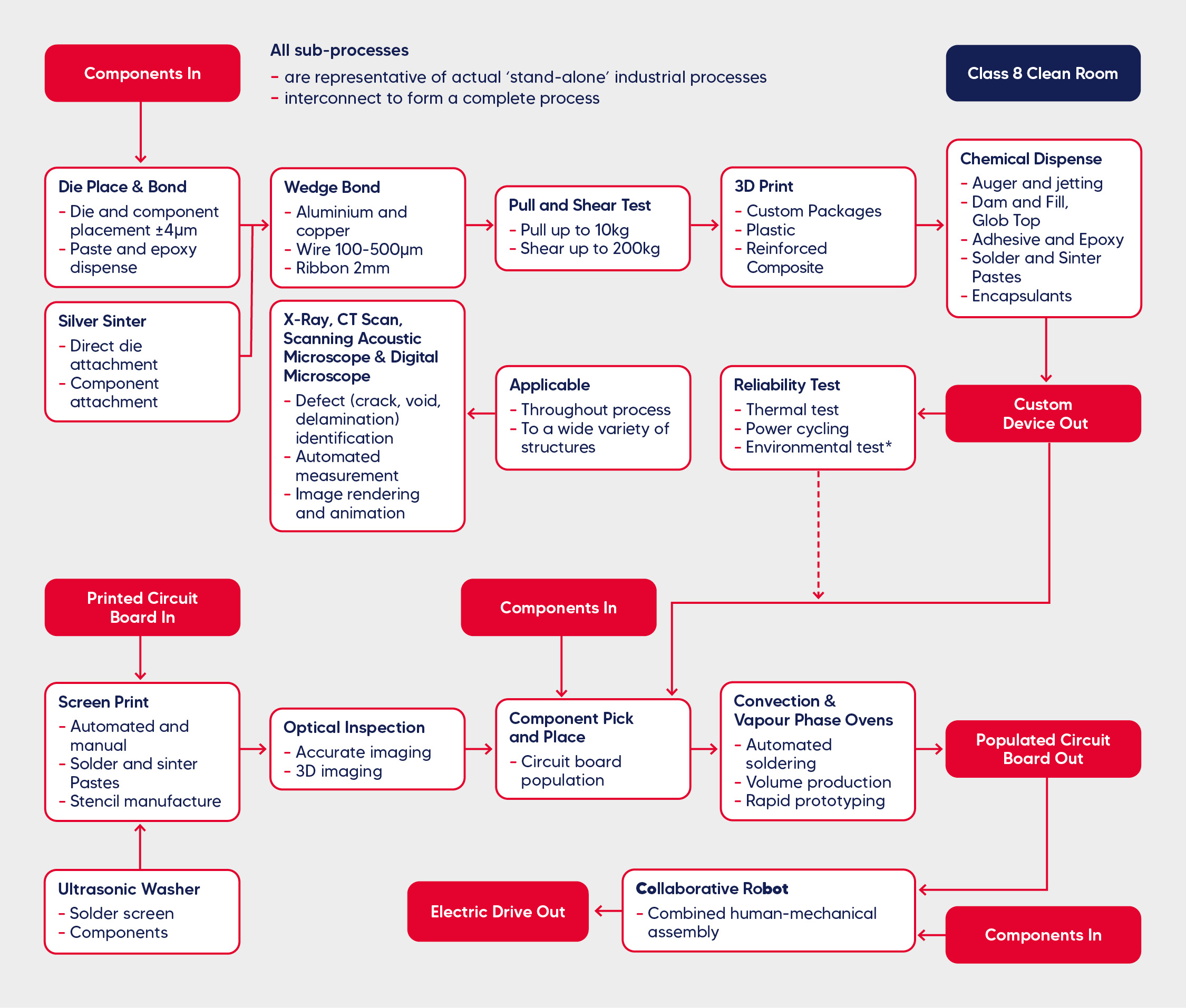
Electrical Machines Assembly Line
The Electrical Machines assembly line includes a range of flexible, automated assembly, and test and measurement equipment, providing an end-to-end platform for electrical machine manufacturing process development.
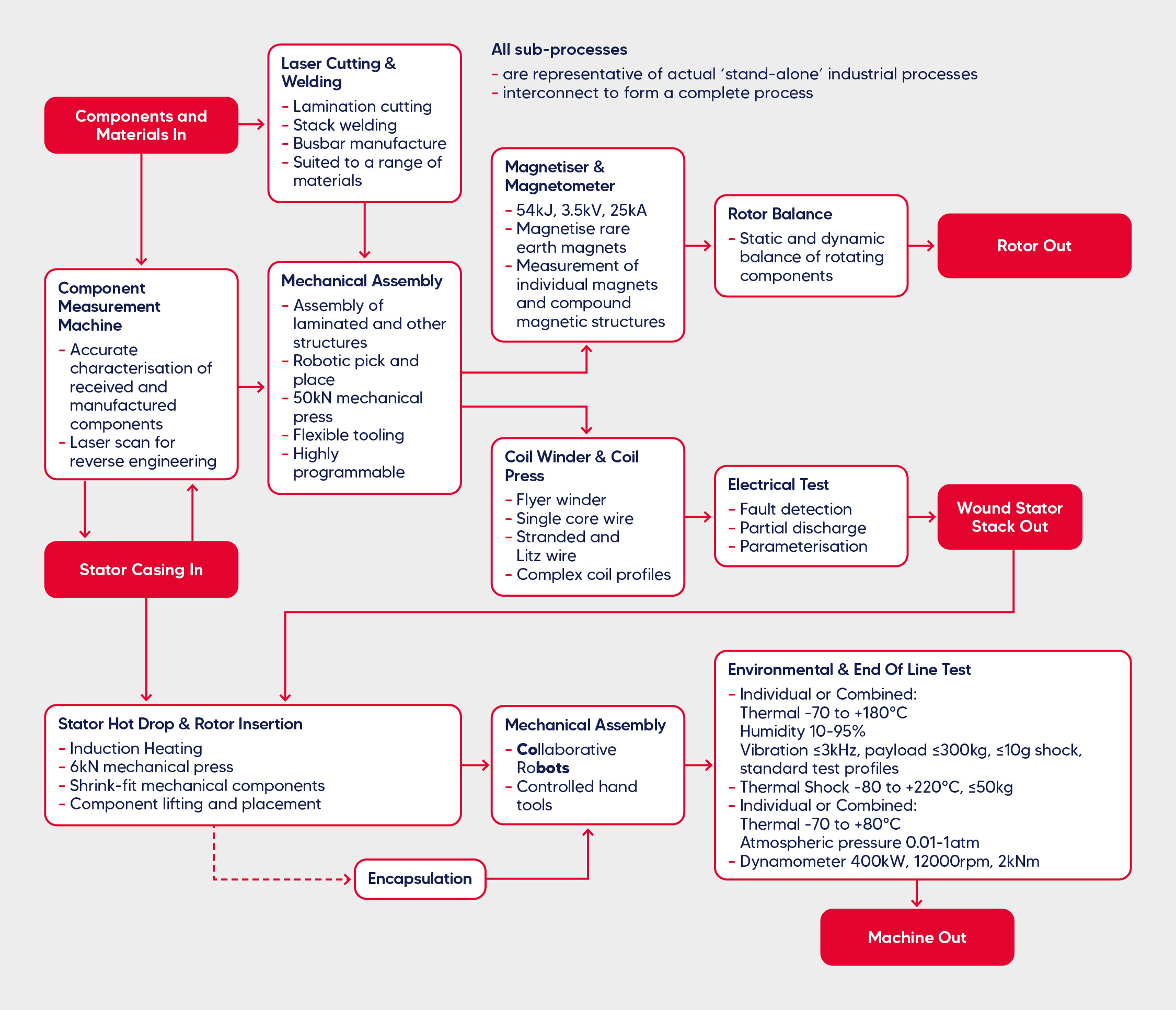
DER-IC University of Sheffield Advanced Manufacturing Research Centre
DER-IC University of Sheffield AMRC has developed the UK’s first open-access Rotor Spin Test Facility for testing electrical machine rotors and other rotating components.
The facility, combined with the AMRC’s advanced manufacturing capabilities, will support the rapid design, manufacture and validation of high-performance machines. By offering high-speed and destructive data-rich testing such as spin balancing, radial growth measurement and fatigue testing, the AMRC plays a key role in helping UK manufacturers drive innovation in next-generation rotating machinery technology – a crucial step for the UK industry’s transition towards net zero.
Rotor Spin Test Facility
Offers high-speed and destructive testing of rotating components: spin balancing; measurement of radial growth; high- and low-cycle fatigue testing; and burst testing with a high-speed camera (up to 160,000 frames per second).