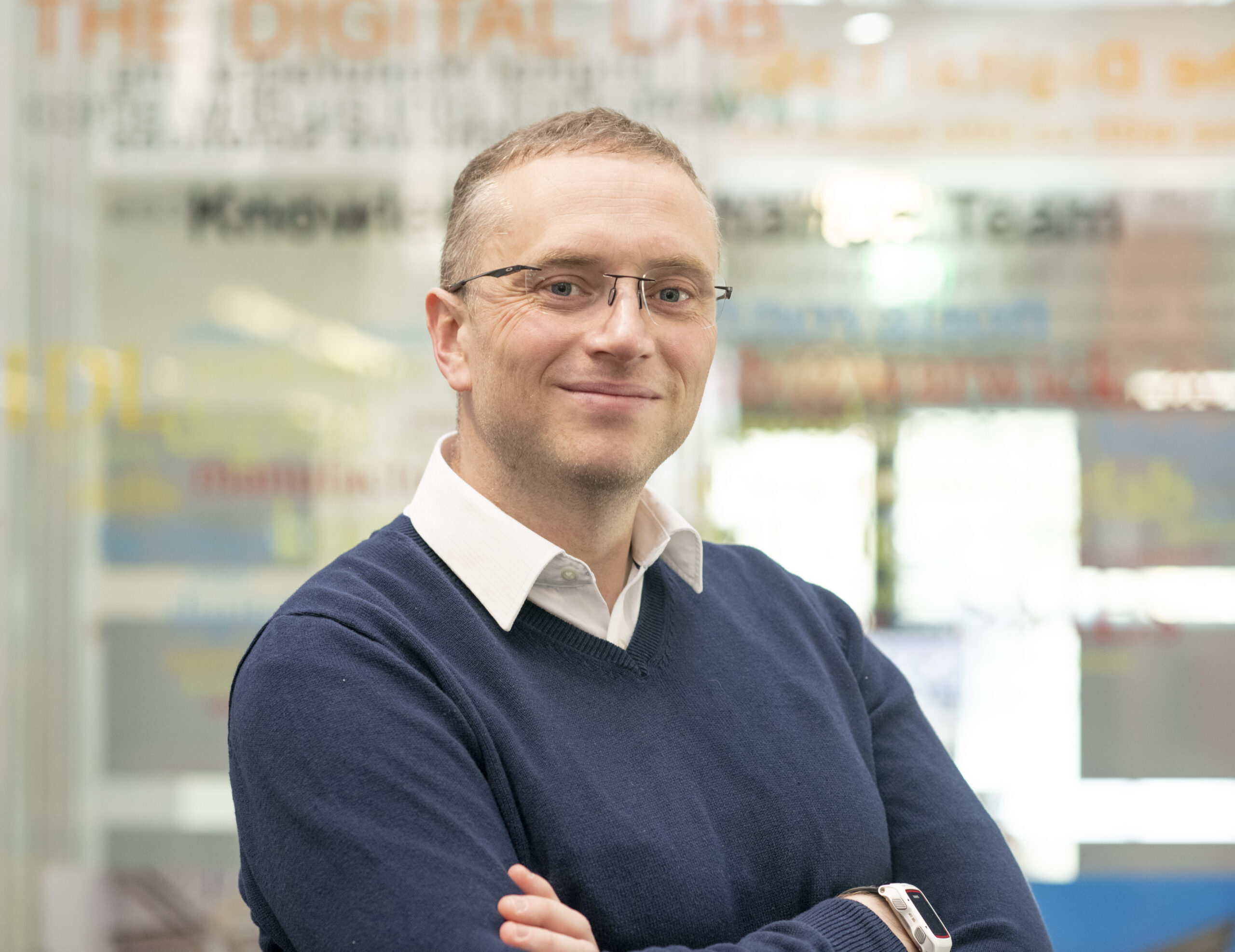
Exclusive Post from The Manufacturer.
Dr Benjamin Silverstone, Associate Professor at the University of Warwick
There is a rightful focus on youth in the race to engage people in electrification technologies. We need their talent, their new ideas, and their understanding of the latest academic research and experimental technology to support the drive towards net zero and cleaner manufacturing practices.
There is however growing concern that we’re sleepwalking into a skills crisis by allowing existing talent to leave the sector en masse. We can’t rely on young people alone to get us to our electrification goals. We need to put some of our attention into the opportunity to reskill and upskill the existing workforce as our economy moves from its mechanical foundations to an electrified future; and we need to discuss how to engage businesses in this process.
The challenge
The Green Alliance, an independent think tank and charity, states that demand is outstripping supply of talent for ‘green jobs’. Whilst job opportunities requiring green skills increased by 8% annually over the last five years, the green talent pool has only grown by 6%. Alongside this, the government also stated that every job has the potential to be ‘green’, which emphasises the size of the education, training and recruitment challenges ahead.
We know that in the drive towards net zero electrification of certain current systems will be a key part of the process. At the launch of the Electric Revolution Skills Hub (ERS Hub) in March 2023, the Government committed £500m to support 169,000 jobs in the zero-emission vehicle industry. This funding is a welcome initial boost to the automotive sector.
Funded by UKRI (UK Research and Innovation) and Coventry University, in partnership with Driving the Electric Revolution Industrialisation Centres (DER-IC), the ERS Hub will offer pathways for people to develop the skills necessary to build a career in power electronics, machines and drives (PEMD).
Although this is a positive step, industry experts believe this is just the tip of the iceberg as electrification is a process that is going to affect a variety of industries across society, including manufacturing, offshore wind, marine, and all areas of land transport and off-highway. These industries are beginning to realise that attrition of experienced workers without secure succession plans to replace them, could have lasting consequences for their future business prospects.
Manufacturing
The pipeline of talent does not meet the current demand, let alone the skills needs in the future. One of the reasons being that the sector has been hit hard by a drop in apprentices joining the ranks, with official figures showing a 28% decrease from 18,680 in 2019-2020 to 13,400 in 2021-2022. Largely made up of young people, apprentices are a key source of talent which need to be replaced.
Offshore wind
The government’s ‘Net Zero Strategy: Build Back Greener (2021)’ outlines the number of professionals needed for each key sector to respond to the net zero challenge. It states that a whopping 97,000 (61,000 direct and 36,000 indirect) are needed by 2030 for the offshore wind industry, an increase of 210% from 31,000 in 2022. The Offshore Wind Industry Council set out to create a meagre 3,000 new apprentices in 2020. Although apprenticeships are great for sector growth, the Build Back Greener strategy states: “We will need tens of thousands of engineers to build and maintain new offshore wind farms”. The strategy also concludes that the median age of workers in the offshore wind sector is 36-40 years, and this is expected to stay the same until 2030. What this shows is there are juniors being trained, albeit not enough, and that we need more experienced workers to be retained, and reskilled to meet the electrification needs of a net zero society.
Automotive
A special report launched in September 2021, The Opportunity for a National Electrification Skills Framework and Forum, highlighted the scale of the electrification challenge and how this would affect the automotive industry and those who currently work in the sector. The report proposed that 63% of current job roles will be subject to change, and for those working with electronic machines this will be higher at 84%. The report predicts that the sector will see a significant amount of competency gaps across many roles, so upskilling experienced workers will be vital. The report also outlines the roles it expects to be affected the most, predicting a 91% change in the knowledge needed by specialist engineers and technicians of power electronics.
Marine and tidal
In a 2022 report, ‘Closing the UK’s green skills gap’, The Green Alliance states that tidal power employment is expected to grow to 4,000 jobs by 2030 and 14,500 by 2040, in manufacturing, installation, operations and maintenance.
The opportunity
The same Green Alliance report predicts that 80% of people who will be employed in 2030 are already in the workforce. This implies that there is already a large group of professionals who could be retrained and upskilled in zero-carbon systems to support the UK to meet its net-zero targets.
In a report from the government’s, Green Jobs Taskforce , it predicts that 1 in 5 (6.3 million) jobs “are likely to be affected by the transition to a green economy”. Not only does retention of skilled worked mean that we are more likely to be able to meet the demands of the net zero challenge, but we can help the UK to continue to compete, grow, innovate and prosper through a well-developed strategy.
With 80% of the future workforce of 2023 already in employment, this is an important and necessary opportunity for the sectors outlined to upskill their current employees, who are highly trained with transferable skills that can be applied to the electrification challenge. Indeed, it is vital companies upskill their employees if the UK has any hope of achieving its long-term climate aspirations.
Reskilling projects in action
At the University of Warwick, funding from the Driving the Electric Revolution (DER) challenge and the High Value Manufacturing Catapult (HVMC) has supported the installation of a new Winding Centre of Excellence at WMG, providing capability for UK based OEMs (Original Equipment Manufacturers) and SMEs (Small and Medium-sized Enterprises) to develop eMachine solutions using discrete hairpin windings. In addition, DER and HVMC funding has provided the School of Engineering at the University with a Power Electronics Reliability and Robustness facility for wind band gap power devices, so critical for enabling the efficient electrification of transport The first of their kind in the UK, these facilities will also be the base for a reskilling project, the Warwick Electrification Deployment (WELD) project, delivered by WMG’s Power Electronics, Machines and Drives (PEMD) Group and the School of Engineering’s Power Electronics group.
The new initiatives include industry workshops, outreach activities in schools and increased teaching provision within PEMD. New content in power electronics, eMachines and drives are created at the University to use current expertise to both up-skill the existing workforce and support the pipeline of talent for future generations. WELD also focuses on the design of IP-free eMachines, with parts manufacture, assembly and testing on campus to allow for hands-on learning.
The trained workforce will help UK businesses to develop and scale new PEMD technologies and manufacturing processes. WELD is funded through the ‘Driving the Electric Revolution: Building Talent for the Future 2’ competition, run by Innovate UK.
We need a plan of action to retain and develop skilled workers
The importance of reskilling experienced workers to meet the demands of the electrification challenge in manufacturing and PEMD is crucial. We need to support those in roles that will ultimately disappear to transition into new roles which support the race for electrification.
The truth is that not everyone will decarbonise without mandate, and the jobs, and organisations that have been staples of the UK economy based on industrialisation, will cease to exist. We’re no longer at the point of usual attrition, this is a pace of change greater than has ever been seen before. We need a solution that is unique in its approach, and this requires collaboration between academia, employers, employees, government and society, to meet this challenge head on. We need champions, big voices, innovative projects, and the funding for employers to deliver this transformation.
It’s not just about decarbonisation, although it’s a huge driver. It’s about growth and innovation and supporting our industrial sectors to thrive with new capabilities and technology that will take them into the next industrial revolution.